Kilncooler Stationary
Infrared controlled
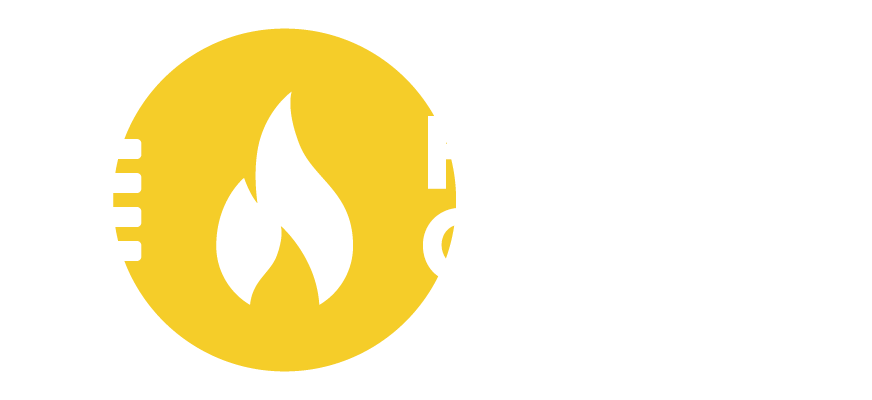
Taking a look at classic solutions
Due to the increasing usage of secondary fuels, which are relatively inhomogeneous, there are more fluctuations in the burning process. This leads to an increased burden on the refractory and the kiln shell—hot spots may occur. In order to reduce this burden, large cooling fans, which blow ambient air, are widely used.
Aircooling using fans has significant disadvantages
- due to the low heat capacity of air a huge throughput is needed
- the consumption of electrical energy is high
- the cooling cannot be targeted specifically to a hot spot on a circumference
- fans emit a substantial amount of noise
Efficiency by water cooling
To overcome these disadvantages KIMA‘s KILNCOOLER uses waterspray nozzles and precise dosing valves, which are controlled by an infrared temperature sensor. The waterspray of an individual nozzle is onlyactivated while its infrared sensor detects a hot spot.
The waterspray cooling is efficient and “on the spot”.
Benefits
- efficient cooling
- flexible usage for hot spots and complete kilns
- ready-to-use modules
- easy installation or relocation
- targeted cooling on kiln‘s circumference
- low noise emission
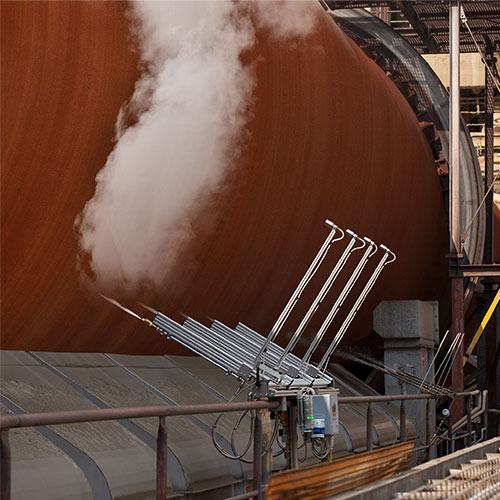
Basic set-up
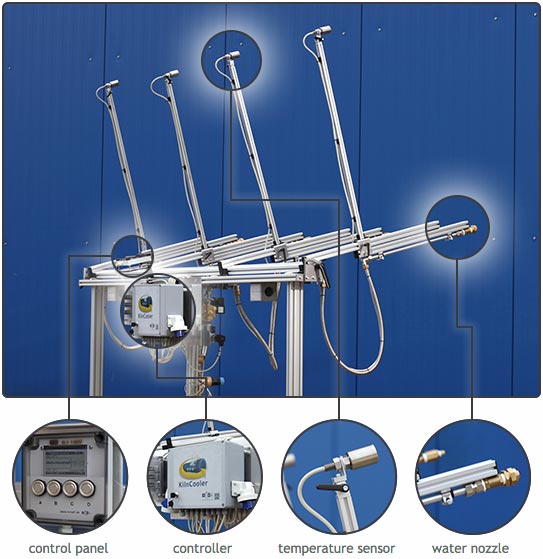
The waterspray is controlled by a FUZZY-controller which uses infrared sensors to precisely locate hot spots on a circumference.
This means: only the hot spot is cooled down, not necessarily the entire circumference.
The “hot spot temperature” can be set individually for every nozzle.
Cooling down a hot spot
With the application of KILNCOOLER, a hot spot can be cooled down rapidly but carefully, avoiding any shrinkage of the kiln shell—cooling rate is up to 2 Kelvin per minute.
After cool-down the shell temperature is kept at its nominal value, thus eliminating mechanical tensions.